Simplicity is the key to successful construction. Structural Insulated Panels can be installed faster and more easily than a stud wall. The double surface spline system with a foam sealing channel makes our system very efficient and simple to install. An experienced crew can expect to enclose a simple 2,000 square foot home in 5-6 working days. Our SIPs can be cut on-site with inexpensive saws or pre-cut at our facility. Pre-cutting prevents on-site waste and it reduces crane rental fees.
SIP’s Are Faster to Construct
One of the best features of building with SIPs is there fast installation time. Indeed, some analysis has shown that the construction time of a SIP building can be shortened from four weeks to one week when compared to a similar stick frame building. In fact, the Energy Studies in Building Laboratory at the University of Oregon conducted extensive testing on the labor requirements of SIPs and determined that SIP homes could be completed in 161 hours less than their equivalent counterparts. This amounted to about 34% less on-site construction time.
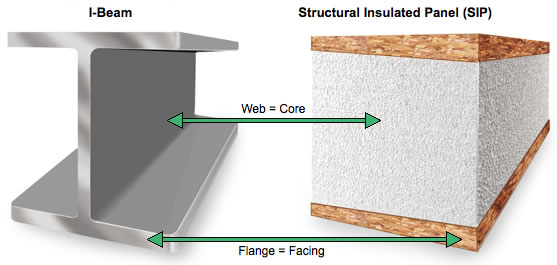
Site Construction Time is Reduced
In the Fall of 1997, Habitat for Humanity built two similar single dwelling family homes, one with SIP panels, and the other with stick frames. The SIP home located in Sedro-Wooley, Washington contained 1,293 square feet and four bedrooms. The 2×4 stick-built home located in Plains, Georgia consisted of 1,064 square feet and four bedrooms. In a report summarizing the findings of the comparison of labor man-hours between the two homes, Habitat for Humanity determined that “the SIP home saved 65% of the site labor when compared to the stick-built home (1).” The reason for this increase in construction efficiency is due to the fact that SIP manufacturers – including Foam Laminates of Vermont – fabricate large sections in their own facility, rather than have carpenters construct the stick framing assembly on-site.
When building with SIPs, on-the site construction time is dramatically reduced and this can have some considerable advantages to the homeowner. For instance, a long fabrication cycle can limit access to construction labor and poor weather conditions can hinder progress. In a time where labor can cost more than the construction materials, perhaps the most alluring feature of SIP buildings is that they can save labor and hence money.
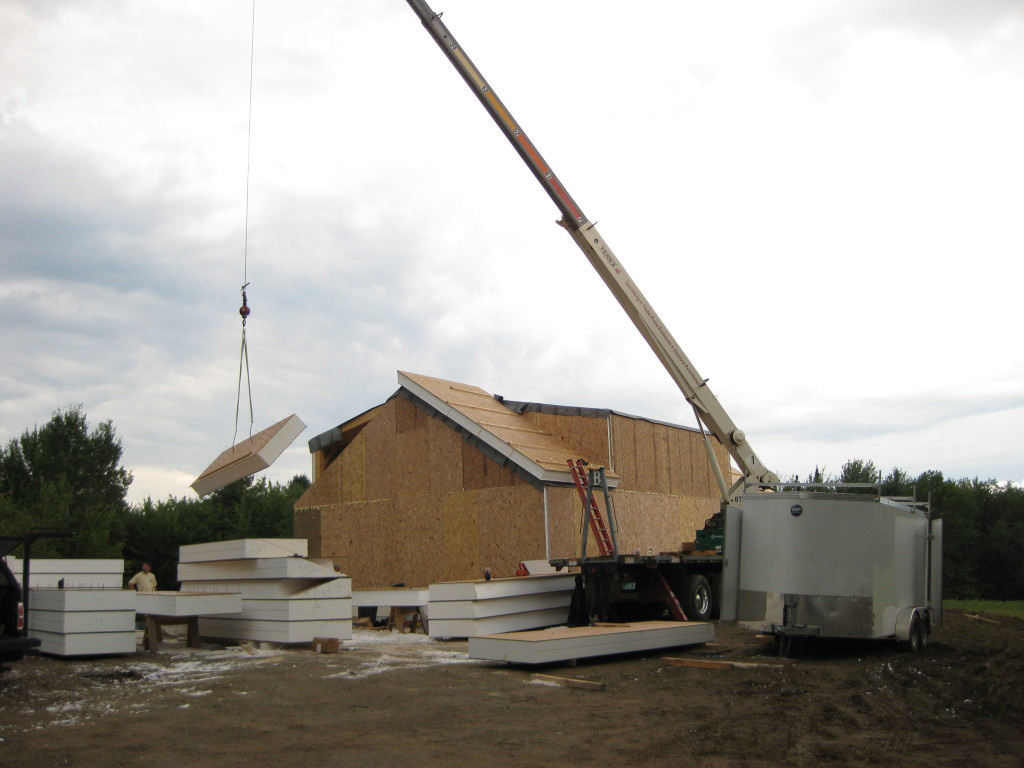
Superior Strength
Recent research has shown that the structural integrity of a SIP building is significantly superior to a conventional stick-framed house in terms of compressive resistance, flexural strength, shear resistance, and uplift resistance. SIPs have undergone exhaustive testing by many third party agencies, and SIPs have proven themselves to be a powerful alternative to the standard fiberglass-stick frame.
If the research wasn’t evidence enough, there are many SIP homes that can be found in the real world, many of which are decades old without any structural damage or weakening. Furthermore, many SIP homes have survived earthquakes and hurricanes in areas where their counterparts: stick-built homes were destroyed. For example, a SIP was struck by the path of a tornado in the town of Clermont, Georgia in March 1998. The tornado destroyed 7 homes in the vicinity, and while the SIP home lost half of its shingles, the house sustained no structural damage.
In another case, a 1993 earthquake shook the ground in Kobe, Japan, crippling a large portion of the city. However, the homes built with SIPs escaped virtually unscathed. Recently, Japan has seen a large boom in SIPs sales and manufacturers, largely in part to this disaster. The ability of a SIP to withstand recent forces of nature is perhaps the true testament to their superior structural performance.
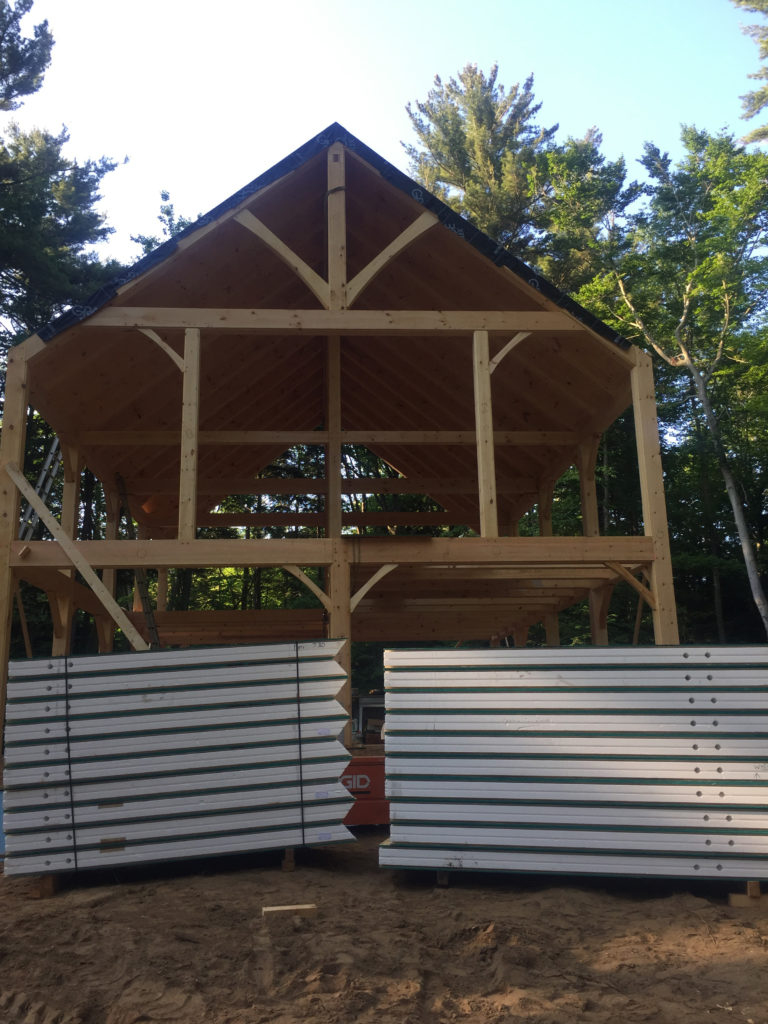
SIP’s Are Straight
If you have ever looked down the length of a stud wall or a piece of dimensional lumber, you will often notice it twists, curves, twists, cups, and bulges. This is often due to moisture penetration, poor storing conditions, and/or inferior quality of lumber. However, this does not occur with SIP panels manufactured by Foam Laminates of Vermont.
We guarantee that you will receive a superior SIP home, one with SIP walls that are square and straight. Why is this important? As any builder can attest, non-straight dimensional lumber can negatively impact any stage of the building process.
Here is a list of some of the advantages our straight SIP walls have over stud walls:
- SIP walls have a continuous wood surface that is crucial for a solid nail-base for both exterior and interior finishes. This is an important feature since the drywall contractor no longer has to search for studs to place fasteners and screws. This allows drywall contractors to complete the work faster and easier resulting in a less expensive and superior final finish.
- Interior finishes such as cabinetry, moldings, flooring, and others can be much easier installed on SIP walls than stud walls since there is a continuous attachment surface. This allows greater design for cabinet makers since they are no longer constrained to expansions ending with studs.
- Heavy picture frames can be installed anywhere on SIP walls and are not limited to stud structures behind the drywall.
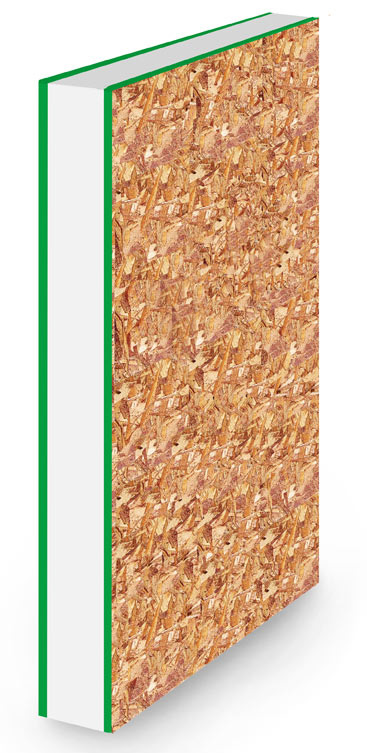
Design Friendly
Most people unfamiliar with the SIP panel building industry confuse it with prefabricated or modular construction technologies. Unfortunately, this mistaken impression has led many to believe that SIP panels are a ‘cheap’ and design limited alternative. However, modular construction methods and SIP panels are two very distinct technologies.
For starters, modular buildings are generally mass-produced in manufacturing facilities to take advantage of cost savings. Modular structures are then transported to the job site and installed. This approach reduces the installation time, but any savings are quickly lost when one considers the difficulties in establishing a vapor barrier since modular homes arrive with trim and siding already completed. This approach makes wrapping a modular home in an effective membrane for airtightness and superior thermal performance, a difficult task.
Modular buildings are prone to the same on-the-site construction difficulties as their counterparts: stick-framed homes. There are problems with making modular structures level, straight, and the transportation to the job site can leave the modular building with weakened joints and non-square corners. These cookie-cutter mass-produced units are limited in design and have therefore transformed America into a series of suburban clones.
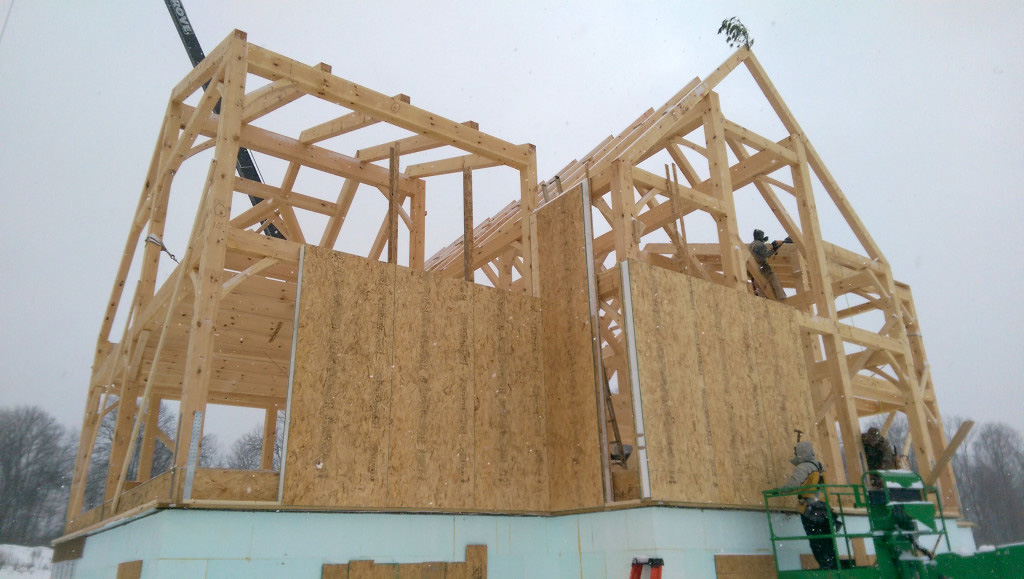
On the other hand, SIP buildings take advantage of the modern approach to building, where communication takes place between the architects, manufacturing companies, and salespeople. The flexibility of CAD programs and speed of fabrication techniques means a project can be conceived, designed, refined, delivered, and assembled in less time than a conventional stick framed building.
Moreover, straight walls and roofs are taken for granted by homeowners. Unfortunately, it is difficult to produce these standards with stick framing. The advantages of a CAD drafting system, the superior continuous expanse of the SIP, efficient spline connections, and today’s highly efficient manufacturing techniques has allowed for SIPs to built to 1/8 inch tolerances, a truly magnificent feat, when one considers the standard for today’s framing tolerances is 1 inch.
The bottom line is that a straight, plumb, and even wall gives a general contractor the best opportunity to do their best work. Additionally, the tightness of the SIP walls results in a virtually airtight thermal blanket with excellent energy efficiency.
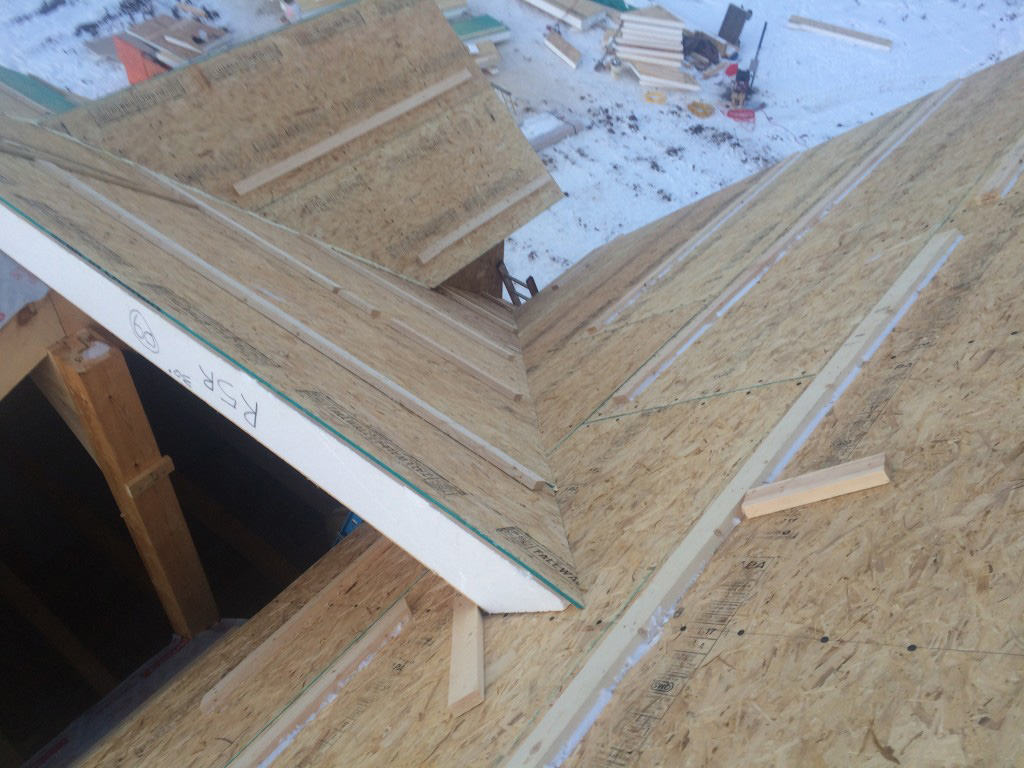